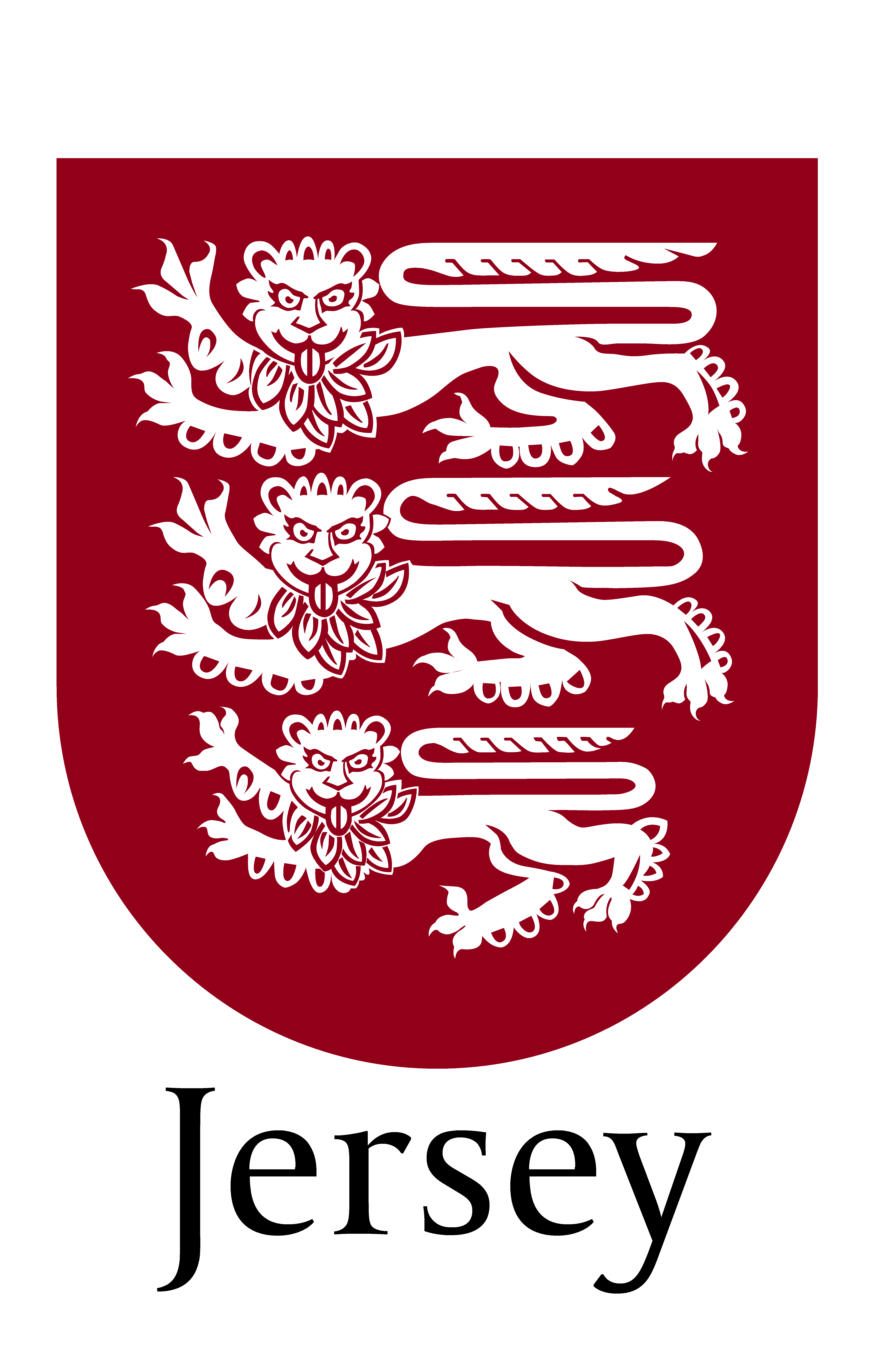
Safeguarding of
Workers (Cranes and Lifting Appliances) (Jersey) Regulations 1978[1]
PART 1
INTRODUCTORY
1 Interpretation
In these Regulations, unless the context
otherwise requires –
“agricultural land” means land, including land under
glass, used by way of trade or business for purposes of agriculture;
“agriculture” includes horticulture, fruit growing, seed
growing, dairy farming, livestock breeding and keeping, the use of land as
grazing land, meadow land, market gardens and nursery grounds;
“approved” means approved for the time being by
certificate of the Minister;
“building operation” means the construction, structural
alteration, repair or maintenance of a building or any appurtenance thereof
(including repointing, redecoration and external cleaning of the structure),
the demolition of a building or any appurtenance thereof, and the preparation
for, and laying the foundation of, an intended building or any appurtenance thereof;
“crane” means an appliance incorporating a structural
member above ground level, or having a jib, and by means of which a load may be
raised, lowered or suspended either by –
(a) a
hook permanently attached to the structural member or the jib; or
(b) a
hook or any other securing device which is suspended from the structural member
or jib by means of a rope or chain which forms an integral part of the appliance
in such a manner as to permit movement of the hook or other securing device in
any direction;
and by means of which the load may be moved from one position to
another by movement of the appliance as a whole, or by movement of the
structural member or jib;
“harbour” includes any port, dock, pier, quay or jetty;
“lifting appliance” means an excavator, fork-lift truck,
mechanical grab, mechanical shovel, piling machine of any description, pulley
or pulley block, a winch which is designed to be used by itself, and any other
prescribed appliance;
“maintained” means maintained in an efficient state, in
efficient working order, and in good repair;
“prescribed” means prescribed by Order;
“safe working load” means the relevant safe working load
required to be specified in the latest certificate issued for the purposes of Regulations
5 and 25;
“work of engineering construction” means the
construction, structural alteration or repair
(including repointing and repainting) or the demolition of –
(a) any
bridge, gas-holder, harbour, pipeline, reservoir,
sewer, sewage works, watercourse or waterworks;
(b) any
steel or reinforced concrete structure, other than a building;
(c) any
road, airfield or sea defence works; and
(d) such
other works as may be prescribed.
2 Application
(1) Subject to paragraph (2),
these Regulations shall apply to any process of raising, lowering or suspending
loads from a crane or lifting appliance, being a process
which involves a risk of bodily injury being caused to persons gainfully occupied
in employment, which is carried out at a place where such persons are so
occupied and in the course of such employment.
(2) These Regulations shall
not apply to agricultural land, except that, where any building operation or
work of engineering construction is carried out on such land, or any part thereof,
these Regulations shall apply to any process mentioned in paragraph (1)
used in connection with such operation or work.
(3) These Regulations shall
not apply to a person by reason only that the person employs another, or is
employed, as a domestic servant in a private household.
3 Obligations
(1) The owner of any crane
or lifting appliance to which these Regulations apply shall comply with the
requirements of Part 2 and Regulations 18 and 28.
(2) Every employer of
workers carrying on any of the processes to which these Regulations apply shall
comply with the requirements of Part 3, except Regulation 20(2), (3)
and (4).
(3) The master or officer
in charge of a vessel shall comply in relation thereto with Regulations 20(2),
(3) and (4) and 26.
(4) Every person employed
shall comply with the requirements of such of these Regulations as relate to
the performance of, or the refraining from, an act by the person and shall
co-operate in carrying out these Regulations and, if the person discovers any
defect in any crane or lifting appliances, shall report such defect without
unreasonable delay to the person’s employer or foreman.
(5) No employer shall allow
a crane or lifting appliance to be used by persons employed by the employer
which does not comply with Part 2 and Regulation 25.
(6) No contractor, employer
or person employed carrying out any operations or works to which these Regulations
apply shall wilfully and without reasonable cause do anything likely to
endanger the contractor, employer, employee or others.
PART 2
CRANES AND LIFTING APPLIANCES
4 Construction and maintenance of cranes and lifting appliances
(1) Cranes and lifting
appliances shall be of good construction and properly assembled,
and shall not be erected or dismantled except under the supervision of a
competent person.
(2) Every part of a crane
or lifting appliance, including any means used for anchoring, fixing or supporting and stabilizing it, the failure of
which would be liable to affect its safe working, shall be –
(a) of
good design, properly made, sound material, adequate strength for the purpose
for which it is used and free from patent defect;
(b) be
properly maintained.
5 Testing and examination of cranes and certain lifting appliances
(1) No crane shall be taken
into use for the first time, or after it has undergone any alterations or
repair likely to affect its strength or stability, unless it has been tested
and thoroughly examined by a competent person and a certificate of such test
and examination containing the approved particulars and signed by the person
carrying out the test and examination has been made.
(2) A crane shall not be
used unless it has been thoroughly examined by a competent person at least once
within the preceding period of 12 months, or at such lesser period as may be
prescribed, and a report of the results of every such examination containing
the approved particulars and signed by the person carrying out the examination
has been made.
(3) If a competent person
making a thorough examination under paragraph (1) or (2) forms the opinion
that a crane cannot continue to be used with safety, the competent person
shall –
(a) immediately
inform both the owner and the user of the crane who shall, on receipt of that
information, cause the crane to be taken out of use; and
(b) forward
a written report to an inspector within 28 days.
(4) If the report of the person
making a thorough examination of a crane under paragraph (2) states that,
in the person’s opinion, it is necessary for the crane to be retested and
thoroughly examined within a specified period of time,
it shall not be used after the period specified in the report has elapsed,
unless it has been retested and thoroughly examined and a certificate issued in
accordance with paragraph (1).
(5) If the report of the person
making a thorough examination of a crane under paragraph (2) states that,
in the person’s opinion, it cannot continue to be used with safety beyond
a specified period of time unless certain repairs are
carried out, it shall not be used after that time until the repairs have been
carried out.
(6) At every fourth
examination made under paragraph (2), the person making the examination
shall state in the person’s report whether, in the person’s
opinion, it is necessary for that crane to be retested and thoroughly examined
as required by paragraph (1) and the period within which this should be
done.
(7) This Regulation shall
apply to a prescribed lifting appliance to such extent as may be prescribed.
6 Stability of cranes and lifting appliances
(1) Appropriate precautions
shall be taken to ensure the stability of a crane or lifting appliance which is
to be used on a surface which is uneven or which is
likely to subside under the weight of the crane or lifting appliance and its
load.
(2) After each erection of
a tower crane, or other crane which is stabilized by portable ballast, on a
site of a building operation or a work of engineering construction, and after
each removal of such a crane about or to such a site, or after any adjustment
to any member of such a crane, being a removal or adjustment which involves
changes in the arrangements for anchoring or ballasting the crane, the security
of the anchorage or the adequacy of the ballasting, as the case may be, shall,
before the crane is taken into use, be tested by a competent person, by the
imposition of –
(a) a
load of 25 % above the maximum load to be lifted by the crane as erected at the
positions where there is a maximum pull on each anchorage; or
(b) a
lesser load arranged to provide an equivalent test of the anchorage or
ballasting arrangements,
and a report of the test containing the approved particulars and
signed by the person carrying out the test shall be made forthwith.
(3) Any portable ballast
used to stabilize a crane shall be properly placed on the crane structure and
be sufficiently secured to prevent it being accidentally displaced.
(4) If a crane’s
stability is secured by means of removable weights, a diagram or notice
indicating the position and amount of the weights shall be fixed on the crane
where it can be readily seen, and each removable weight shall be marked with
its own weight.
(5) No crane shall be used
or erected in weather conditions likely to endanger its stability.
(6) As soon as practicable
after a crane has been exposed to weather conditions likely to have affected
its stability, the anchorage arrangements and ballast shall be examined by a
competent person, and the crane shall not be used again until all steps
necessary to ensure its stability have been taken.
(7) A suitable level
indicator shall be permanently fitted to every mobile crane, other than a crane
which travels on a line or rails, and shall at all
times be clearly legible to the crane operator from the crane operator’s
operating position in the cabin.
7 Travelling cranes
(1) Without prejudice to Regulation
4, all rails on which a crane moves shall –
(a) be
supported and secured to a base or foundation in such a manner as to prevent
any movement of the rails sufficient to endanger the safe use of the crane;
(b) have
an even surface where in contact with the wheels of the crane;
(c) be
provided with stops or buffers of adequate strength at each extremity of use.[2]
(2) Adequate measures shall
be taken to ensure that the rails are kept free from any object or material
liable to cause danger by obstructing the rails.
8 Overhead travelling cranes
(1) If any person is
employed or working on or near the wheel track of an overhead travelling crane
in any place where the person would be liable to be struck by the crane,
effective measures shall be taken by warning the operator of the crane, or
otherwise, to ensure that the crane does not approach within 20 feet (6100
mm) of that place.
(2) If any person is
employed or working otherwise than as mentioned in paragraph (1), but in a
place above floor level, where the person would be liable to be struck by an
overhead travelling crane, or by any load carried by such a crane, effective
measures shall be taken to warn the person of the approach of the crane, unless
the person’s work is so connected with or dependent on the movement of
the crane as to make a warning unnecessary.
9 Coupled cranes
(1) Where 2 cranes are
required to raise or lower a single load –
(a) the
lifting operation shall be planned in advance;
(b) a
competent person shall be appointed to supervise the lifting operation and
shall be present throughout the operation;
(c) so
far as is practicable, cranes of equal capacity and similar design shall be used;
(d) the
lifting operation shall be so arranged that the load on each crane shall not
exceed 3/4 of the safe working load of the crane.
(2) More than 2 cranes shall
not be used to raise or lower a single load.
10 Marking of safe working loads
(1) The safe working load
and distinguishing number or mark shall be marked on every crane, winch,
pulley, pulley block, fork-lift truck and any prescribed lifting appliance.
(2) Every crane having a
safe working load which varies according to the operating radius or inclination
of the jib shall be fitted with an accurate indicator which shows the operating
radius and inclination of the jib for the time being, so that the safe working
load corresponding to the operating radius or inclination of the jib is shown
on the indicator, or can be calculated by reference to tables provided in the
operator’s cabin of the crane which have been prepared by the maker of the
crane or by a competent person.
(3) The indicators and
tables mentioned in paragraph (2) shall be properly maintained and shall at all times be clearly legible to the crane operator
from the crane operator’s operating position in the cabin.
(4) Tables which are provided
in accordance with paragraph (2) shall have suitable and sufficient
entries to enable an operator to determine the safe working load of the crane
at any operating radius or any position of the jib within the range of
operating radii or angles of inclination of the jib.
11 Automatic safe load indicators
(1) Every crane of a
prescribed type or class shall, within the prescribed period, be fitted with an
automatic safe load indicator of an approved type.
(2) Every automatic safe
load indicator shall be tested and thoroughly examined by a competent person
every 6 months, and shall be tested by a competent person before the crane to
which it is fitted is next taken into use after –
(a) the
crane has been wholly or partially dismantled; and
(b) after
any erection, alteration, or removal of the crane likely to have affected the
proper operation of the indicator.
(3) A report of the results
of any test or thorough examination required by this Regulation containing the
approved particulars and signed by the person carrying out the test or thorough
examination shall be made forthwith to the owner of the crane.
12 Safe access to and egress from cranes or lifting appliances
(1) A safe means of access
and egress with, where necessary, adequate hand holds
and foot holds shall be provided for –
(a) the
operator of a crane or lifting appliance; and
(b) any person
engaged on the examination, lubrication or repair of a crane or lifting
appliance where it is possible for that person to fall a
distance of more than 6 feet 6 inches (1980 mm).
(2) No ladder, or run of
ladders, forming an integral part of a crane or
lifting appliance and which rises a vertical distance of more than 30 feet
(9140 mm), shall be used, unless there is provided an intermediate landing
place or places, such that the vertical distance between any 2 successive
landing places does not exceed 30 feet.
(3) Every landing place to
which paragraph (2) applies shall be of adequate dimensions and, except
where it is necessary to provide access for the ladder, shall be provided with
secure fencing at least 3 feet (920 mm) in height, consisting of upper and
lower rails and placed so as to prevent, so far as
possible, persons from falling.
(4) Every vertical ladder
to which paragraph (2) applies shall be fitted with guard hoops of
adequate strength spaced at suitable intervals along the ladder.
13 Brakes, controls and other safety devices
(1) Every crane or lifting
appliance, other than a crane or lifting appliance which is hand-operated in
such a way that the operator can control the load, or a lifting appliance which
is self-sustaining, shall be provided with an efficient braking system which
shall be capable of sustaining anything being raised, lowered
or suspended within its capacity.
(2) Every lever, handle, switch or other device provided for controlling the
operation of any part of a crane or lifting appliance and whose accidental
movement or displacement is liable to cause danger shall, where practicable,
unless it is so placed or the appliance is so constructed as to prevent
accidental movement or displacement, be provided with a suitable spring or
other locking arrangement to prevent the accidental movement or displacement.
(3) Every lever, handle, switch or other device provided for controlling the
operation of any part of a crane or lifting appliance, other than the rotating
handles for raising or lowering the load on a winch or non-derricking jib crane
not operated by mechanical power, shall have on or adjacent to it clear
markings to indicate its purpose and mode of operation.
14 Cranes with derricking jibs
Every crane with a derricking jib which is operated through a
clutch, other than a crane in which the hoisting drum and the derricking drum
are independently driven, or the mechanism driving the derricking drum is
self-locking, shall be provided with an effective interlocking arrangement
between the derricking clutch and the pawl sustaining the derricking drum which
shall ensure that –
(a) the clutch cannot be
disengaged unless the pawl is in effective engagement with the derricking drum;
and
(b) the pawl cannot be
disengaged unless the clutch is in effective engagement with the derricking
drum.
15 Precautions where crane or lifting appliance has travelling or
slewing motion
Without prejudice to the requirements of Regulation 7, on every
stage gantry or other place where a crane or lifting appliance having a
travelling or slewing motion is in use, an unobstructed passageway not less
than 2 feet (610 mm) wide shall be maintained between any part of the appliance
liable so to move and any guard rails, fencing or other object that may cause a
trap, and if, at any time, it is impracticable to maintain such a passageway at
any place, all practicable steps shall be taken to prevent the access of any person
to that place at that time.
16 Cabins for operators of cranes
Every crane shall have a suitable cabin for the operator which
shall –
(a) afford the crane
operator adequate protection from the weather; and
(b) where reasonably
practicable, be provided with suitable means of heating which does not result
in the escape within the cabin of any injurious or offensive fumes:
Provided that these requirements shall not apply if the person
operating the crane is protected from the weather by a building or other
structure, or the crane is used only occasionally, or for short periods.
17 Powers of inspectors to require cranes and lifting appliances to be
tested
If an inspector has reasonable grounds for considering that a crane
or lifting appliance may not continue to be used with safety, the inspector
may, by notice served on the owner of the crane or lifting appliance, require
it to be tested and thoroughly examined, in the manner required by Regulation 5(1),
by a competent person chosen by the inspector, and the crane or lifting
appliance shall not be used after the date of service of the notice unless it
has been thoroughly examined and tested in the manner aforesaid and certified
by the competent person as being safe for further use.
PART 3
LIFTING OPERATIONS
18 Operators of cranes and certain lifting appliances
No crane, excavator, fork-lift truck, mechanical grab, mechanical shovel or piling machine shall be operated by any person
unless –
(a) the person’s
employer, or the owner of the crane or appliance, has certified that the person
is competent for the purpose; or
(b) the person is operating
the crane or appliance for training purposes under the direct and constant
supervision of a person who has been so certified,
and the employer or owner, as the case may be,
shall keep available for inspection by an inspector any certificate
given under this Regulation.
19 Signalling
(1) If the person operating
a crane has not a clear and unrestricted view of the load, or, where there is
no load, of the point of attachment for a load, and of its vicinity throughout
the operation, except at any place where such view is not necessary for safe
working, there shall be appointed, and suitably stationed, one or more
competent persons as may be necessary to give necessary signals to the
operator.
(2) Every signal given by a
signaller for the movement or stopping of a crane shall be distinctive and
shall be clearly audible or visible to the person to whom it is given.
(3) The operator shall obey
only the signals of the person appointed to give the signals, except that the
operator must obey a signal for an emergency stop given by any person employed.
20 Safe means of access and egress and safe place of work for persons
engaged in lifting operations
(1) A safe means of access to
and egress from their place of work shall be provided for all persons who are
engaged in lifting operations.
(2) In the case of lifting
operations which are carried out on board a vessel, safe access to and egress
from the vessel shall be provided for the persons engaged on such operations by
such one or more of the following means as is suitable and sufficient in the
circumstances, that is to say –
(a) gangways;
(b) the
ship’s accommodation ladders,
and, insofar as it is not reasonably practicable to provide either
of those means, one or more ladders of adequate strength.
(3) Every gangway,
ship’s accommodation ladder and ladder provided under paragraph (2)
shall be –
(a) of
good design, properly made, sound material, adequate strength for the purpose
for which it is used, and free from patent defect;
(b) properly
maintained;
(c) adequately
secured; and
(d) adjusted
as often and to such an extent as is necessary to ensure that it is kept at a
safe angle of inclination to the horizontal.
(4) No gangway or ship’s
accommodation ladder provided under paragraph (2) shall be used
unless –
(a) it is
of sufficient width for the purpose for which it is used and
in any case not less than 22 inches (560 mm) wide;
(b) it is
fenced throughout its length on each side to a height of at least 3 feet (920 mm)
by means of upper and lower rails or taut ropes or chains or by other equally
safe means.
(5) Without prejudice to
the preceding paragraphs, every place at which any person works in connection
with operations involving the use of cranes and lifting appliances shall, so
far as is reasonably practicable, be made and kept safe for any person working
there.
21 Load not to exceed safe working load
No crane or lifting appliance, other than an excavator or a
mechanical grab, shall be loaded beyond its safe-working load, except for the
purpose of testing the crane or appliance as required by Regulation 5, or for
the purpose of testing an automatic safe load indicator as required by Regulation
11(2).
22 Attendance at suspended loads
No load shall be kept suspended from a crane or lifting appliance,
unless there is a competent person at the controls of the crane or appliance
while the load is suspended.
23 Secureness of loads
(1) Every part of a load
shall be securely held or supported whilst being raised, lowered
or suspended and shall be adequately secured to prevent danger from slipping or
displacement.
(2) Where a load is liable,
whilst being moved on a crane or lifting appliance, to come
into contact with, and to displace, any object, measures shall be taken
to prevent the danger so far as is reasonably practicable.
(3) No bale, crate or
similar package shall be raised, lowered or suspended
by means of any band, strap or wire forming part of that bale, crate or package
unless it has been specially designed for that purpose.
24 Teagle openings and similar doorways
(1) Every teagle opening or
similar doorway used for raising or lowering goods or materials, whether by
mechanical power or otherwise, shall be securely fenced and shall be provided
with a secure hand hold on each side.
(2) The fencing shall be
properly maintained and shall, except when the raising or lowering of goods or
materials is being carried on at the opening or doorway, be kept in position.
25 Carrying of persons
(1) No power-driven lifting
appliance shall be used for carrying any person.
(2) No person shall be
carried by a crane except –
(a) in a
suitable chair, skip or other receptacle of at least 3 feet (920 mm)
internal depth; or
(b) on a
stage or platform each side of which is provided with secure fencing at least 3
feet (920 mm) in height consisting of upper and lower guard rails, and
toe-boards not less than 6 inches (155 mm) in depth, all of which are an
integral part of the stage or platform,
and which is suspended from the hook of the crane.
(3) When a person is
carried from a crane by an appliance complying with paragraph (2) –
(a) effective
measures shall be taken to prevent the appliance from spinning or tipping in a
manner liable to be dangerous to that person;
(b) effective
measures shall be taken to ensure that the appliance is attached to the crane
hook in such a way that it cannot be accidentally displaced;
(c) the
appliance shall be –
(i) of good design,
properly made, sound material, adequate strength for the purpose for which it
is used, and free from patent defect,
(ii) properly
maintained, and
(iii) inspected
by a competent person before being taken into use for the first time on any day
on which it is used;
(d) before
being taken into use for the first time after manufacture, or after it has
undergone any alterations or repairs likely to affect its strength, the
appliance shall be tested and thoroughly examined by a competent person and a
certificate of such test and examination containing the approved particulars
signed by the person carrying out the test and examination and specifying the
safe working load shall be obtained;
(e) the
appliance shall be marked with its safe working load, its own weight and the
maximum number of persons it is permitted to carry;
(f) the
appliance shall not be used to carry any load or materials, other than those
required for the immediate use of the persons using it, and the combined weight
of the person or persons and any load or materials carried shall not exceed its
safe working load;
(g) the
crane by which the appliance is carried shall be fitted with limit switches
which automatically stop –
(i) the hoisting, and
(ii) where
appropriate, the derricking motion of the crane,
when the hook or jib, as the case may be, reaches the upper and
lower safe limits of movement, but which allow the movement of the crane to be
reversed after they have actuated;
(h) the
operator of the crane shall not leave the controls of the crane unattended.
(4) If more than one person
is carried by an appliance, complying with paragraph (2), one person on
the appliance shall be detailed to give any signals necessary for its safe
movement and the operator of the crane shall obey the signals of that person
alone, except that the crane operator shall obey any emergency stop signal
given by any person employed whether carried on the appliance or not.
(5) No appliance used for
carrying persons in accordance with this Regulation shall be loaded beyond its
safe working load, except for the purpose of testing.
26 Cranes and cargo winches forming part of the permanent equipment of
vessels
A crane or cargo winch which forms part of the permanent equipment
of a vessel shall not be used in any lifting operation unless it complies with
the requirements of the appropriate provisions of the Protection Against
Accidents (Dockers) Convention (Revised) 1932 of the International Labour
Organization.
PART 4
MISCELLANEOUS
27 Certificates of exemption
The Minister may, subject to such conditions, if any, as may be
specified therein, by certificate in writing, which the Minister may at his or
her discretion revoke at any time, exempt from all or any of the requirements
of these Regulations –
(a) any premises or any
class or description of premises;
(b) any machinery, plant,
equipment or appliance or any class or description of machinery, plant, equipment or appliance; or
(c) any work or any class
or description of work,
if the Minister is satisfied that the requirements in respect of
which the exemption is granted are not necessary for the protection of persons
employed or are not reasonably practicable.
28 Reports and other documents
Every report and record made and all
certificates and particulars given in pursuance of any requirements of Parts 2
and 3 shall be kept readily available for inspection by an inspector and by any
person who is responsible for complying with those Parts and shall be kept for
a period of 4 years after the date to which the reports and other documents
relate.
29 Orders
(1) The Minister may make Orders
for prescribing anything which, under these Regulations, the Minister is
required or authorized to prescribe.
(2) [3]
30 Citation
These Regulations may be cited as the Safeguarding of Workers
(Cranes and Lifting Appliances) (Jersey) Regulations 1978.